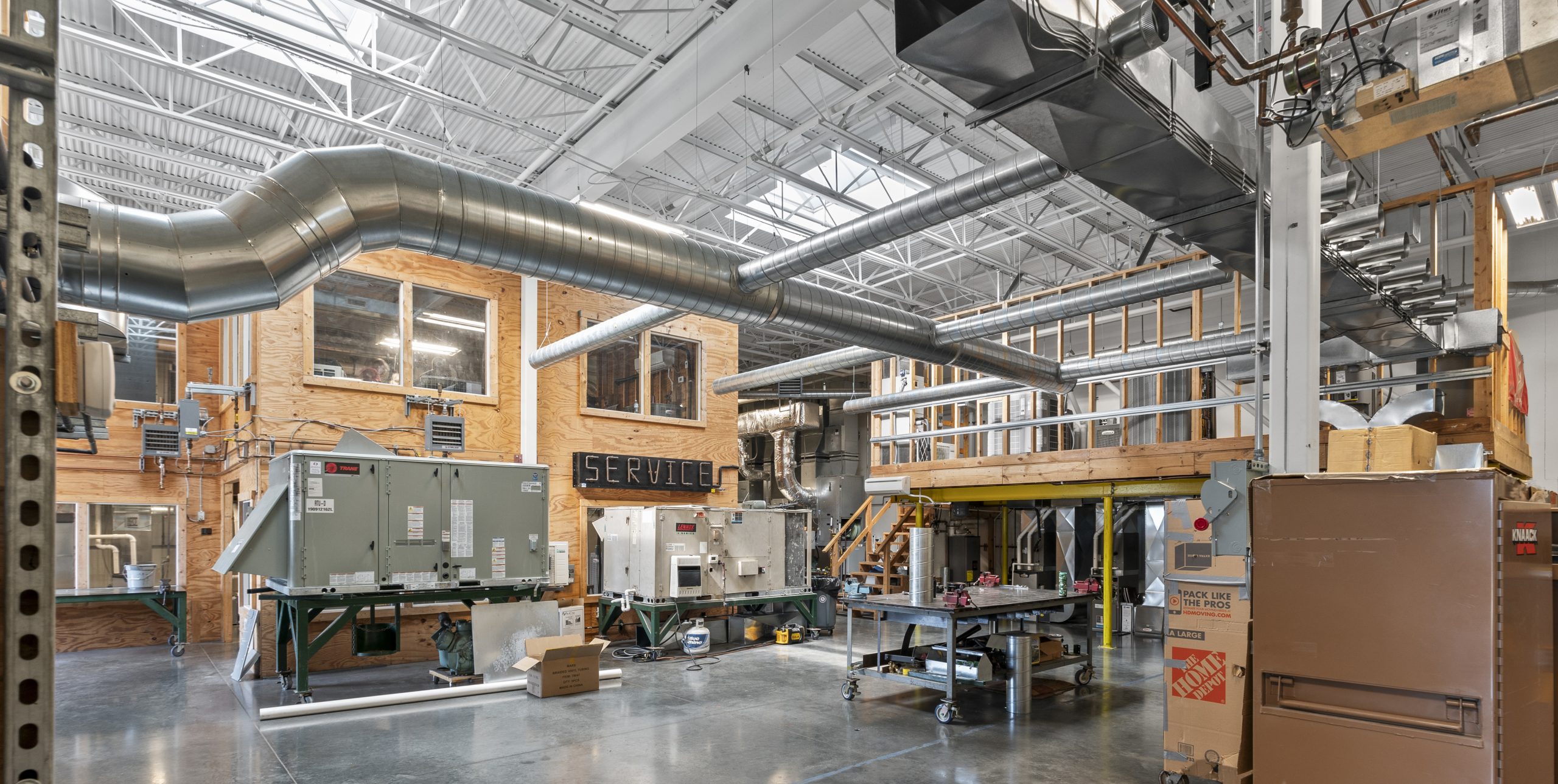
Shaping Energy Efficiency:
Sheet Metal Workers Turn to Keystone
When Sheet Metal Workers’ Local 36 St. Louis headquarters opened in 2012, it was a model of sustainability and energy efficiency. The 95,333-square-foot training facility included solar panels on the roof, renewable interior materials, and a Crestron lighting control system. It was St. Louis’ highest-rated LEED structure.
Its lighting, however, was provided by fluorescent tubes. And that became an issue.
The Challenge:
Ten years ago, fluorescent was a logical decision: LED was still an emerging and relatively unproven technology. But the fluorescents, dependent on ballasts, tended to burn out, said Rob Weber, the building’s facilities manager.
“A lot of the lights are on motion sensors and timers, and they set the timers as short as possible,” said Weber. “In the high traffic areas that doesn’t work very well with fluorescent lights on ballasts, so we had a lot of ballasts going out.”
Initially, Weber simply replaced or rewired the affected fixtures to bypass the ballast. That had its own drawbacks, he noted. The updates created a patchwork of different CCT outputs with the original lamps, and negatively affected the working and training atmosphere for the occupants.
“The lighting was getting uneven,” said Weber.
“Being end-user driven, Keystone has the most encompassing product availability,” he said. “I can do both fixtures and lamps, interior and exterior, all through the same line.”
Andrew Boerschig, Project Manager at Guarantee Electrical Company
The Solution from Keystone:
So when the opportunity arose to redo the whole building with LED, he jumped at it.
The impetus was a discussion of upgrading the building’s solar array. A solar rep for contractor Guarantee Electrical Company, which had handled the electrical and lighting for the project in 2012, met with Weber and noted that the fluorescent lighting negated the potential savings of replacing and adding solar panels. Turning to LED and going with ballast-bypass UL Type B tubes was the logical move, said Andrew Boerschig, project manager with Guarantee Electrical.
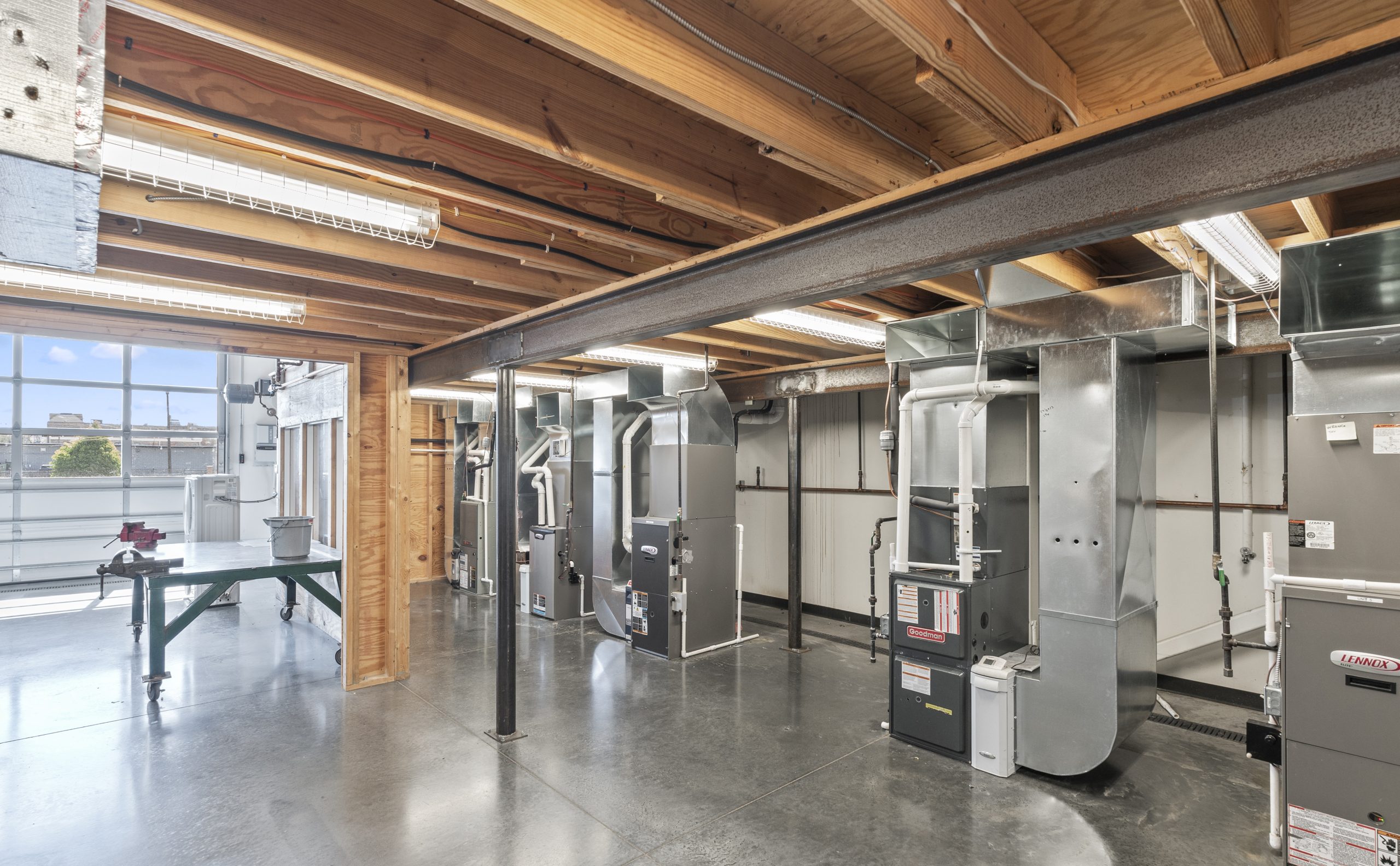
“We walked the facility and used the existing plans as a jumping-off point,” Boerschig recalled. “All of the fixtures were in pretty good shape, so it was truly just an LED retrofit project.”
Weber added that the timing was right. Ameren, the local power company, has a rebate program for LED lighting upgrades, and the project was a perfect fit.
“The present lighting is going away anyway, and while we could do it now and get the rebate from Ameren for them to pay a quarter of it, it made financial sense to just do it and be done with it,” he said.
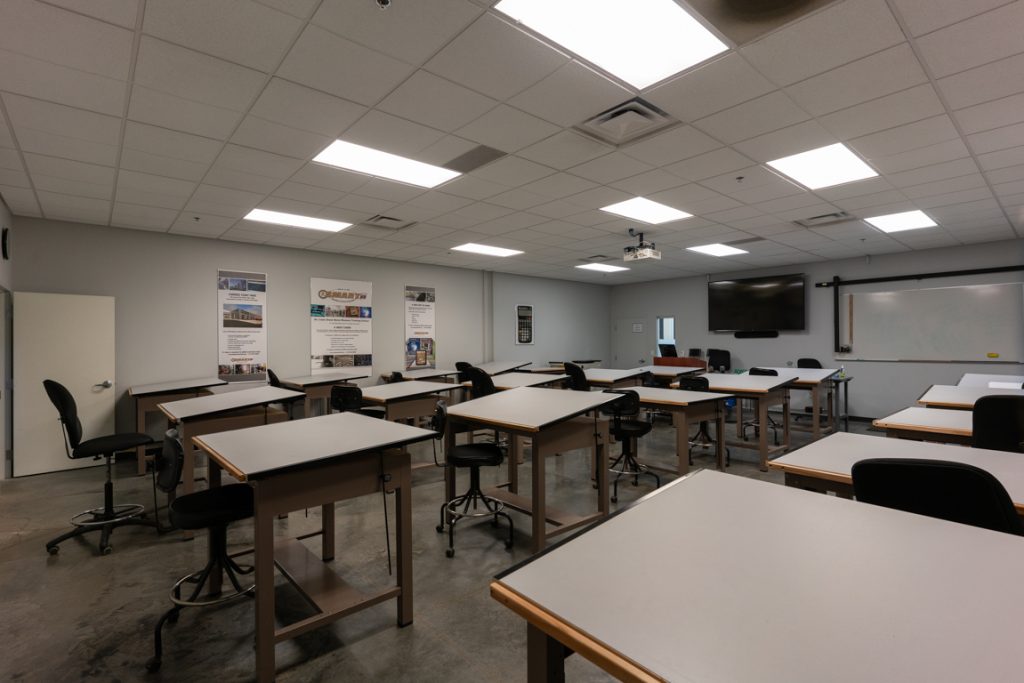
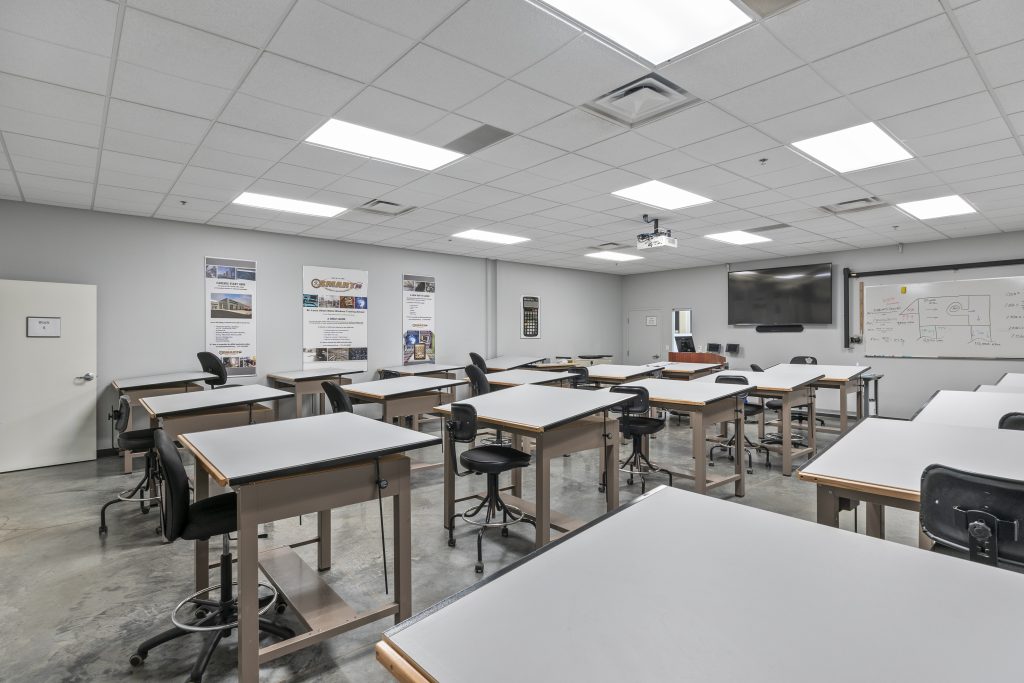
the space is brighter and offers a friendlier ambience.
Keystone was the preferred partner for the plan, said Boerschig. Fast shipping from Keystone’s Kansas City warehouse meant Guarantee had the product in 48 hours, and the wide range of lamps made inventory selection a snap.
For Sheet Metal Local 36, Boerschig kept it simple. For most of the lighting, he opted for a combination of 25W 4-foot T5 and 10.5W 4-foot T8 UL Type B LED lamps to eliminate ballasts, mindful of them as a failure point. He stuck with UL Type A 4-pin lamps for decorative fixtures with unique components to avoid compatibility issues, though he expects those will be changed to ballast-bypass lighting in the coming years. In addition, Boerschig chose lamps with a dedicated 3500K CCT to maintain a consistent lighting atmosphere agreeable to staffers and visitors.
All Keystone products came through St. Louis-based distributor Holt Electrical Supply.
Installation went quickly. Even with rewiring, the job took about six weeks—on time, without interfering with work and classes at the facility, and ahead of a major conference for the sheet metal workers.
“We hit a home run, and the timing was perfect,” said Boerschig.
The Results:
Available Rebates
Ameren, the local power company, provided a $20,064 rebate for the retrofit—almost 25% of the overall project cost.
Energy Efficiency
The project will pay for itself in just 2 ½years and save more than 262,000 kWh of electricity.
An Ideal Atmosphere
Even with a similar CCT to the legacy lighting, the overall environment feels brighter and meshes better with the natural light, said Weber: “You definitely see a color difference, especially in the shop areas.”
Local 36’s Weber praises the results. He commented that new lighting has allowed people to see better, making the facility experience better for employees and training.
And with the lighting taken care of, he can focus on other maintenance items, keeping the LEED-certified building at peak efficiency, instead of being distracted by yet another failed ballast.
Boerschig couldn’t be happier with how everything turned out. He appreciates Keystone’s dependability and service.
Just the reliability and knowing everything’s going to work—it gives us some legitimacy. Keystone is such a trusted partner, and the teamwork ensures that the whole project will be top-quality.
Andrew Boerschig, Project Manager at Guarantee Electrical Company
Keystone Products Used:
- T5 LED Lamp (KT-LED25T5HO-48GC-835-DX2)
- T8 LED Lamp (KT-LED10.5T8-48G-835-DX2 /G2)
- Emergency Back Up (KT-EMRG-LED-5-500-AC)
- 2-Pin CFL LED Lamp (KT-LED82P-H-835-D)
- 4-Pin CFL LED Lamp (KT-LED94P-H-835-S)